Известно, что одним из параметров, определяющих долговечность эксплуатации прибора, является стойкость к коррозии. Поэтому для увеличения его срока службы необходимо, чтобы используемые для изготовления материалы обладали высоким химическим сопротивлением при различных внешних условиях.
Автор: А.Г. РАКОЧ, д.х.н., проф., НИТУ «МИСиС» (г. Москва); А.А. ЛОБАЧ, к.т.н.; В.В. БЕГНАРСКИЙ, к.т.н., ЗАО «РИФАР» (г. Гай, Оренбургская область) Развитие отопительной техники у нас и за рубежом за счет усовершенствования конструкции, материалов, применения современного оборудования и технологий производства, эффективных методик испытания и способов контроля привело к значительному повышению показателей качества, эксплуатационных свойств, технических характеристик. Однако не все вопросы остаются решенными, что замедляет дальнейший прогресс в этой области. Известно, что одним из параметров, определяющих долговечность эксплуатации прибора, является стойкость к коррозии. Поэтому для увеличения его срока службы необходимо, чтобы используемые для его изготовления материалы обладали высоким химическим сопротивлением при различных внешних условиях [1]. В большом ряде случаев для изготовления внутренней поверхности каналов трубчатых, панельных, секционных радиаторов отопления, полотенцесушителей и других приборов системы отопления, по которым циркулирует теплоноситель — вода, используют чугуны, стали и алюминиевые сплавы. Все они подвержены коррозии по внутренней поверхности, которая может усиливаться при наличии воздуха. Скопление воздуха в отопительном приборе возможно при работе его в системе индивидуального или коллективного водяного отопления. Наличие воздуха в отопительном приборе не только приводит к ускорению коррозионных процессов, но и ухудшает технические характеристики, благоприятствует негативным побочным явлениям работы, таким как шум. При установке и заполнении отопительного прибора причинами присутствия воздуха в нем является то, что он не был полностью удален из общей системы отопления или происходит его накопление в процессе эксплуатации. В зависимости от качества подготовки теплоносителя по количеству растворенных газов, а также величин давления и температуры в конкретное время и в данном месте системы отопления [2] объем воздуха может меняться в сторону увеличения или уменьшения, что усложняет количественный анализ. Попытки устранить этот воздух из системы отопления в целом, в т.ч. и из отопительного прибора, не всегда являются эффективными. Для удаления воздуха из отопительного прибора используют автоматические или ручные воздухоотводчики или воздухоспускные клапаны [3]. Работа любого воздухоотводчика для радиаторов отопления основана на открытии и закрытии небольшого отверстия, через которое скопившийся газ выходит из внутренней полости отопительного прибора в атмосферу. По конструкции ручные воздухоотводчики, их еще называют краном Маевского, представляют собой радиаторную заглушку с клапаном, работа которого основана на открытии или закрытии сквозного отверстия путем вращения специальной ручки или винта. Ручные воздухоотводчики имеют простую, относительно надежную конструкцию, невысокую стоимость, но требуют от пользователя ответственного обращения. К сожалению, при ручном спуске воздуха нет возможности оценить объем воздуха внутри радиатора. Поэтому воздух может быть спущен не полностью. В результате в радиаторе отопления может присутствовать воздух и в системе «газ–теплоноситель» (электролит) протекают коррозионные процессы. Причинами, из‑за которых скопление воздуха в радиаторе отопления может вызывать интенсивную коррозию углеродистой стали, являются: конденсация паров, приводящая к различной толщине слоя влаги на различных участках поверхности стали (образование микрогальванических элементов); работа микро‑ или макрогальванических элементов на участках поверхности стали, разделенных ватерлинии.
Образование микро‑ и макрогальванических элементов обуславливается различной скоростью переноса деполяризатора (О2) к различным участкам металлической поверхности, находящимся под разным по абсолютной толщине слоем электролита. Примером автоматического воздухоотводчика может быть клапан с поплавковым механизмом. Работа этого устройства основана на автоматическом открытии и закрытии спускного отверстия с помощью поплавкового клапана. При отсутствии воздуха в отопительном приборе поплавок держит выпускной клапан закрытым. Если появляется воздух в канале радиатора, уровень воды понижается, поплавок отпускается, тем самым открывая выпускной клапан, через который воздух выводится из радиатора. Несмотря на привлекательность автоматических воздухоотводчиков, они не лишены недостатков. К недостаткам можно отнести то, что они имеют сложную конструкцию. Последнее повышает их стоимость. Кроме того, в случае неправильной установки, вследствие циклических нагрузок (особенно превышающих предельно допустимые), высока вероятность их выхода из строя. Выпускной канал автоматических воздухоотводчиков часто приходит в аварийное состояние — подтекает, заиливается, загрязняется, особенно в системах отопления с плохим качеством теплоносителя. Известно, что отопительные приборы можно классифицировать по преобладающему способу теплоотдачи и по используемому материалу [2]. Рассматривая влияние скопления воздуха в отопительном приборе на коррозию и поиск решения этой проблемы, классификацию можно расширить по такому конструктивному критерию, как форма и схема соединения внутренних каналов, по которым движется теплоноситель. Так как от этого зависит не только траектория движения теплоносителя, но и геометрия, а также расположение так называемых застойных зон с воздухом. Для большинства известных схем подключения радиаторов отопления, участки в которых скапливается воздух — это крайние участки верхнего горизонтального канала, которые не имеют входного или выходного узла подключения. В связи с вышеизложенным в данной работе изучали коррозионное поведение внутренней поверхности радиаторов при различных температурах, имитируя их поведение на примере образцов, изготовленных из качественной углеродистой конструкционной стали (далее — конструкционная сталь). Образцы размещали над теплоносителем (электролитом), а также частично или полностью погружая в него. Углеродистая сталь выбрана в связи с тем, что имеет высокую коррозионную стойкость в щелочных водных растворах в широком температурном интервале [5] вследствие ее пассивирования при таких внешних условиях. Кроме того, в данной работе были проведены ускоренные электрохимические испытания углеродистой стали в теплоносителе при различных его температурах. Образцами являлись пластины, вырезанные из горизонтального канала радиатора отопления диаметром 30 мм. Средние геометрические размеры образцов: 25 × 50 × 2,5 мм. Модельный раствор теплоносителя готовили в соответствии с нормами, правилами эксплуатации и требованиями к подготовке теплоносителя систем отопления, тепловых сетей РФ (СО 153-34.20.501–2003) путем растворения гидроксида натрия в дистиллированной воде до достижения раствором значения величины pH = 9. Величину pH контролировали с помощью pH‑метра с погрешностью ± 0,2. Коррозионные испытания проводили при температуре 25 ± 2 °C и 80 ± 2 °C. При проведении данных ускоренных коррозионных испытаний образцов были использованы четыре различные схемы расположения образцов в коррозионной среде: образец полностью погружен в раствор при отсутствии доступа воздуха к раствору (коррозия в термически деаэрированной среде); образец полностью погружен в раствор, свободный доступ воздуха к раствору (коррозия в аэрированной среде); образец расположен в атмосфере над раствором (атмосферная коррозия в парах воды над раствором); образец погружен в электролит приблизительно на 50% (поверхность раздела раствор/воздух).
Величина скорости коррозии образцов из углеродистой стали в исследуемых растворах была определена гравиметрическим методом (ГОСТ 9.908–85). На аналитических весах с пределом допускаемой погрешности ± 0,002 г были измерены массы образцов до и после проведения коррозионных испытаний после удаления с их поверхности продуктов коррозии. Продукты коррозии с поверхности образцов удаляли в соответствии с ГОСТ 9.907–83 механическим методами. Геометрические размеры образцов в ходе испытания измеряли при помощи штангенциркуля. По величине убыли массы (Dm, г), площади образцов (S, м2) и времени экспозиции испытания (t, ч) рассчитывали отрицательный показатель изменения массы: Km = Dm/(S t), г/(м2⋅ч). По величине отрицательного показателя изменения массы рассчитывали глубинный показатель коррозии (П): П = Km /(8760rFe), мкм/год, где rFe = 7,874 г/см3 — плотность железа. При электрохимических испытаниях устанавливали свободный потенциал коррозии и снимали анодные поляризационные кривые углеродистой стали в аэрируемом и деаэрируемом модельном растворе теплоносителя при температурах 25 ± 2 °С и 80 ± 2 °С. Испытания проводили, используя цифровой потенциостат, трехэлектродную ячейку с двойными стенками, подключенную к термостату. В качестве вспомогательного электрода использовали платиновый, а электрода сравнения — хлорсеребряный. Из экспериментальных данных (рис. 1) следует, что углеродистая сталь при ее полном погружении как в деаэрируемый, так и аэрируемый щелочной (pH = 9) водный раствор при температуре 25 и 80 °C находится в пассивном состоянии. На образцах отсутствуют следы коррозионных поражений после выдержки в щелочном электролите в течение 217 ч, а потенциалы коррозии (рис. 1) более чем на 380 мВ положительнее обратимого потенциала Fe при всех выбранных при данном исследовании температурах электролита. 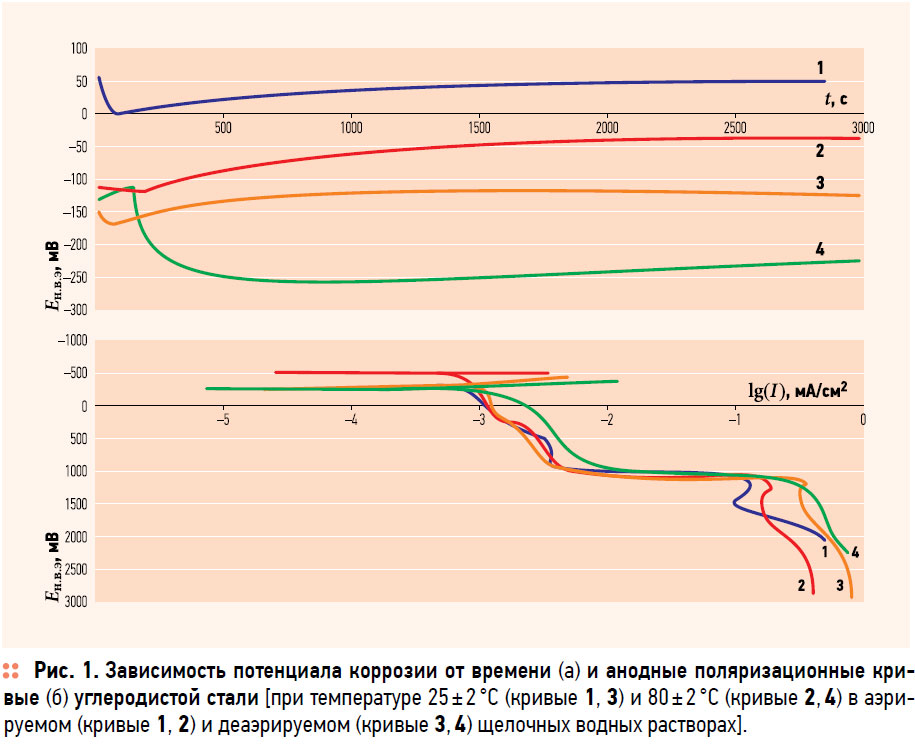
Согласно диаграммам Пурбе* (рис. 2) на поверхности углеродистой стали при заданных внешних условиях может формироваться оксид Fe2O3 или гидроксид железа (Fe(OH)3). 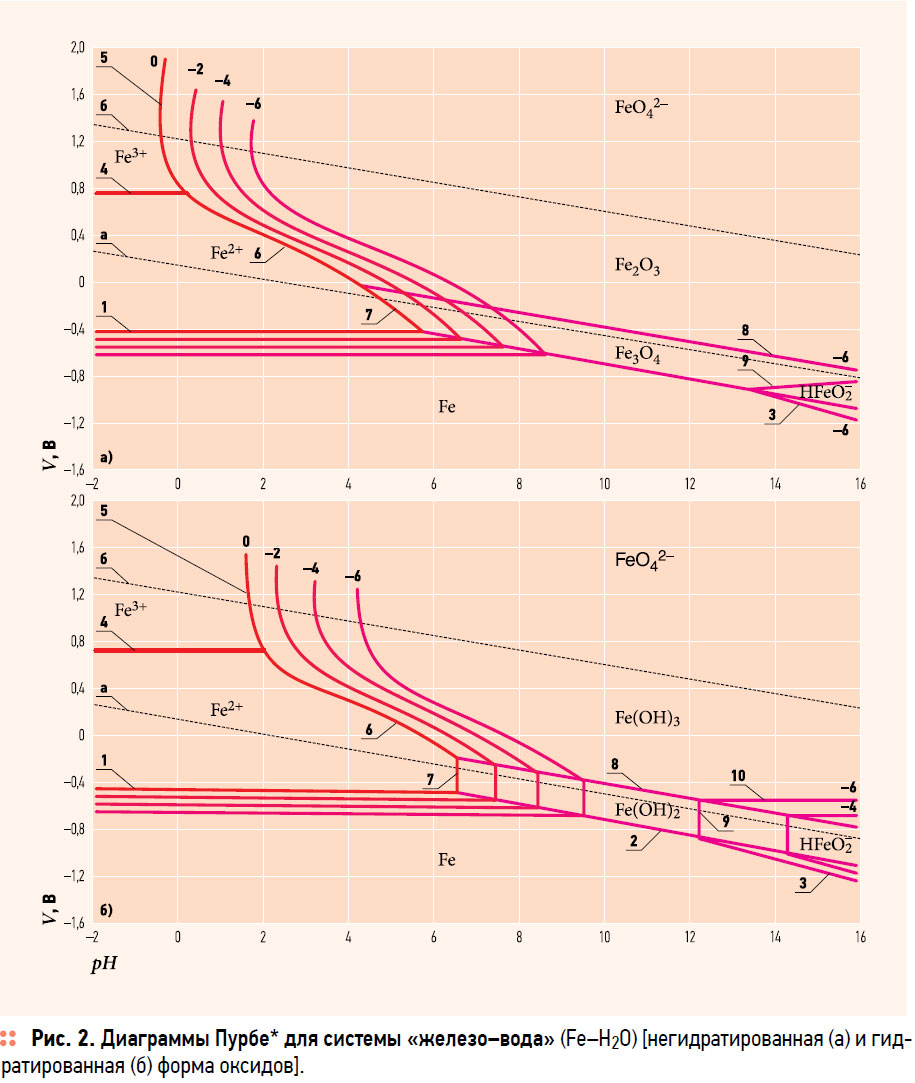
Следовательно, коррозионная стойкость углеродистой стали, вследствие ее пассивирования в щелочном водном растворе как при комнатной температуре, так и при температуре 80 °C, является высокой, и ее можно использовать для изготовления отопительных приборов. Однако, коррозия исследуемой стали, очевидно, как и других углеродистых сталей, в значительной степени должна возрастать при ее частичном погружении в щелочной водный раствор или при ее нахождении над ним на расстоянии, когда реализуется конденсация паров воды на ее поверхности, и, что особенно опасно, приводить к локальным видам коррозии. Локальные виды коррозии реализуются, как правило, когда значительно большая поверхность металлического материала находится в пассивном состоянии; т.е. образуется гальваническая пара: «пассивная поверхность (катод) — активные, как правило, небольшие участки металлической поверхности (анод)». При этом, практически, не происходит торможение (перенапряжение) катодного процесса, а анодный ток, протекая через небольшие участки поверхности, приводит к их интенсивной коррозии (большая плотность тока на этих участках). Действительно, из экспериментальных данных (рис. 1) следует, что на поверхности углеродистой стали, находящейся над электролитом, температура которого 25 °C, появились относительно небольшие коррозионные пятна. С увеличением температуры электролита до 80 °C на поверхности стали образовались коррозионные язвы. Несомненно, причиной этих локальных коррозионных поражений углеродистой стали является образование микрогальванических пар. Образование аэрационных пар [4, 5] происходит вследствие различной скорости переноса кислорода к разным участкам металлической поверхности. Участки поверхности с относительно тонким слоем электролита на них являлись катодами, а участки поверхности, покрытые более толстым слоем влаги, — анодами. С увеличением температуры водного раствора интенсивность работы микрогальванических элементов возрастает по экспоненциальному закону, так как лимитирующей стадией под тонким слоем электролита является, как правило [4, 5], кинетическая стадия — катодная реакция: О2 + 2H2O + 4е = 4ОН–. Работа гальванических элементов (микро-, а также макрогальванических) является значительно более интенсивной, если образец из углеродистой стали находился не над щелочным водным раствором, температура которого 80 °C, а был частично погружен в данный электролит. Большая часть поверхности образца, находящаяся над ватерлинией, являлась в основном катодом, а погруженная в электролит — анодом. В соответствии с представлениями Н.Д. Томашова и Г.П. Черновой [5], при интенсивной скорости протекания катодного процесса может происходить смещение потенциала коррозии в положительную сторону до потенциала перепассивации. При этом потенциале происходит вторичное активирование металлической поверхности вследствие протекания анодной реакции, приводящей к растворению пассивной пленки: Fе3+ + 4Н2О → FеO4 2– + 8Н+ + 3е. Следует отметить, что локальные анодные участки имелись и на не погруженной в водный раствор поверхности образца. Очевидно, что на этих участках поверхности углеродистой стали слой электролита являлся более толстым — заторможен перенос кислорода к этим участкам металлической поверхности. Перепассивация участка металлической поверхности, находящейся в щелочном водном растворе, происходит только при высокой температуре электролита (80 °C), когда интенсивно протекает катодный процесс на остальной поверхности образца. Только на участке металлической поверхности, не погруженной в электролит, появились коррозионные пятна. В табл. 1 приведена оценка коррозионной стойкости образцов из углеродистой стали в щелочном (pH = 9) водном растворе по десятибалльной шкале (табл. 2) в зависимости от их расположения в коррозионной среде и температуры электролита. 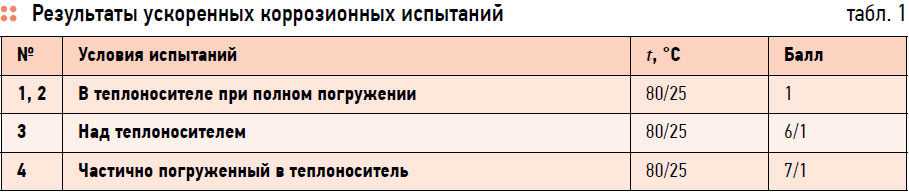
Представленные результаты распространяются на все отопительные приборы, в которых присутствует воздух. 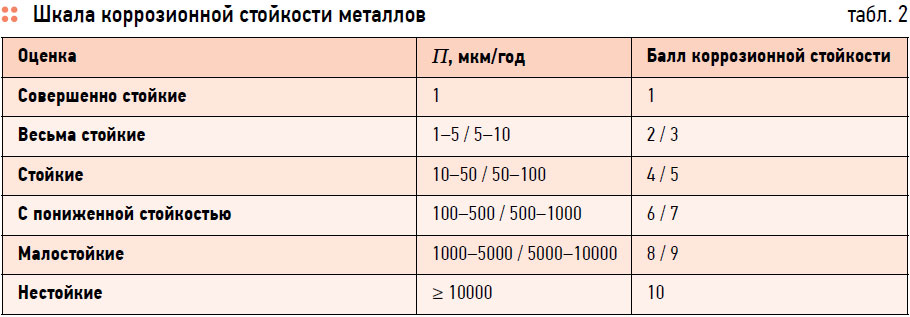
При использовании очень тонкой стенки стальных каналов, малоэффективных способов спуска воздуха, некачественной подготовки теплоносителя локальная коррозия достаточно высока, чтобы может приводить к быстрому выходу из строя отопительных приборов. При работе отопительных приборов рекомендуется использовать эффективный воздухоотводчик, а также проводить оценку скопления воздуха внутри него. Выводы Показано, что недопустимо скопление воздуха в отопительных приборах из‑за протекания в щелочном водном растворе локальной коррозии углеродистой стали на участках поверхности, прилегающих к ватерлинии. Интенсивная локальная коррозия протекает вследствие возникновения микро- и макрогальванических элементов под различными слоями влаги на участках поверхности стали, расположенных по обе стороны ватерлинии. При этом анодными являются те участки поверхности, к которым затруднен доступ кислорода.
1. Пахомов В.С., Шевченко А.А. Химическое сопротивление материалов и защита от коррозии. — М.: Химия, КолосС, 2009. 2. Сканави А.Н., Махов Л.М. Отопление: Учебник для ВУЗов. — М.: Издательство АСВ, 2008. 3. Невзоров А. Автоматические и ручные воздухоотводчики, их назначение и применение // Акваерм, №4/2004. 4. Жук Н.П. Курс теории коррозии и защиты металлов. — М.: Металлургия, 1976. 5. Томашов Н.Д., Чернова Г.П. Теория коррозия и коррозионностойкие конструкционные сплавы / Уч. пособие для ВУЗов. — М.: Металлургия, 1993.
|